Maintenance Made Easy
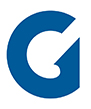
by Matt Molnar - Product Support Specialist On Dec 21, 2017, 03:00 AM
Subscribe To Aerial Pros
Filter by tags
Equipment maintenance vs. rental: The delicate balance every rental company plays. If a piece of aerial lift equipment isn’t out in the field, it’s not making money, so you want it out on the job as much as possible.
How do you keep the equipment in the field? You maintain it. However, inspections and maintenance procedures take time and can delay a piece of equipment from getting back into the game.
As enticing as it may be to look past scheduled maintenance and maintenance items to get the equipment back on the jobsite, don’t fall into temptation. Failure to properly conduct maintenance procedures can result in poor equipment performance, component damage and unsafe operating conditions. Maintaining equipment is essential for safe operation, machine performance and long service life. As we all know, equipment that performs well in the field, leads to happy customers, future rental business and continues to generate revenue.
In order to keep a happy maintenance/field-revenue-generating balance, you need to do a little homework when selecting aerial lift equipment and partner with a manufacturer who understands this need. Genie takes pride in designing and building machines that require minimal maintenance, and we heavily invest in engineering, testing and manufacturing aerial lift equipment that delivers dependable operation on the jobsite and can be easily maintained. That way it can be put back out on rent in the shortest time possible.
When it comes time to do those maintenance inspections, Genie makes it as easy as following a checklist. What’s better, any qualified team member with a working knowledge of the equipment can perform the inspection, so there is no delay in waiting on a licensed mechanic, who may be tied up on a higher priority project.
The Genie® checklists divide maintenance procedures into four simple-to-follow subsections – Commissioning, Quarterly, Annually and Programmed – so maintaining our equipment fast and easy. To review the required maintenance inspection items and to print out a hard copy of the checklist, follow the links below:
Boom maintenance inspection form: http://manuals.gogenielift.com/Parts%20And%20Service%20Manuals/data/Service/forms/02_MaintInspecForm_Booms.pdf
Scissor maintenance inspection form: http://manuals.gogenielift.com/Parts%20And%20Service%20Manuals/data/Service/forms/02_MaintInspecForm_Scissors.pdf
Telehandler Inspection form: http://manuals.gogenielift.com/Parts%20And%20Service%20Manuals/data/Service/forms/02_MaintInspecForm_Telehandlers.pdf
You can also find these forms in the maintenance manual shipped with each piece of equipment. These pages can be copied and handed to the technician as a checklist record of the inspection. Remember, completed reports should be kept for a minimum of four years, or as long as necessary, to remain in compliance with company policies, jobsite requirements and governmental regulations/requirements.
Related Posts
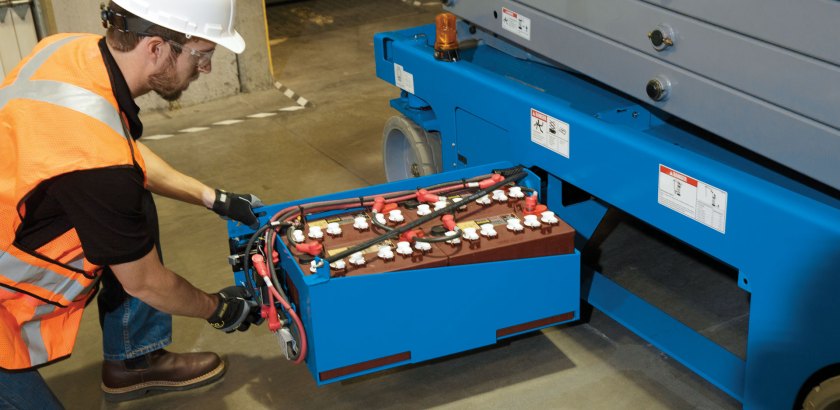
Aerial Battery Maintenance Tips
A well maintained battery can yield up to three times longer equipment life.
Continue Reading
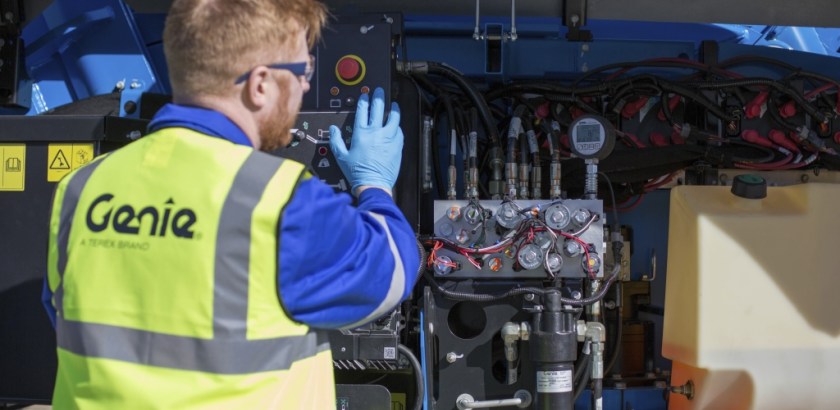
Maintenance Tips for Your Tier 4 Final Aerial Work Platforms
After decades of preparation, aerials with Tier 4 Final engines are beginning to find their way into your rental fleets.
Continue Reading
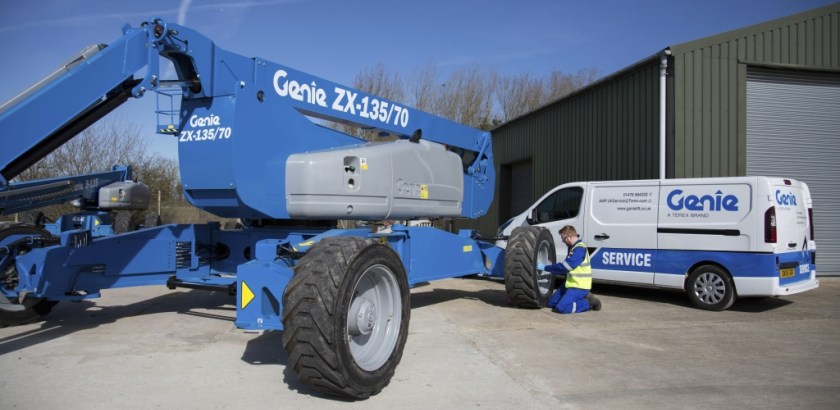
Controlling Maintenance Repair Time is Key to Lowering Fleet Costs
Controlling the cost of your rental fleet is important to be a profitable rental company, but where do you begin?
Continue Reading