Service Minute: Aerial Equipment Reliability Tips
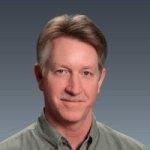
by Ron Wixon - Customer Satisfaction Manager On Sep 21, 2018, 03:00 AM
Subscribe To Aerial Pros
Filter by tags
Having worked in the Genie® field and phone support for over 20 years, I’ve noticed a couple of things about machine reliability: It’s simple to help ensure mobile elevating work platforms (MEWPs) perform consistently and for a very long time. For example, many Genie lifts manufactured 1980s are still in operation in the field thanks to savvy ownership.
To increase your equipment’s reliability and productivity in the field, please follow these best practices for care of your MEWP:
Periodic maintenance
More than check-the-box exercise, scheduled inspections and preventative maintenance is the number one way to help guarantee the best performance from your equipment. It enables you to identify small problems before they grow and down your unit. For example, minor damage to a component, like a leak in a hub that will grind up if unchecked, damage in a boom tube that becomes a crack, or a neglected cable adjustment that allows a cable to jump off the sheave, are all preventable. Potential reliability issues are cheaper and easier to fix the earlier they’re spotted.
OEM parts
To maximize your rental return on invested capital (rROIC), look to the original equipment manufacturer (OEM), including Genie, for the best ways to keep your rental fleet up and running. When it comes to replacement parts, the individual costs may seem small, but you know that their impact on a machine’s uptime is enormous.
Replacement parts that aren’t factory-fitted might physically fit, but they may not work as well and often cause downtime. Joysticks, for example, can cause issues — they can be the wrong style, that either doesn't work with your unit, work poorly (operating in one direction but not another) or for a very short period of time.
Because MEWPs are some of the most frequently requested and rented equipment in your fleet, you don’t have the time or money to deal with downtime and failures caused by parts that aren’t specified for your Genie machine. This can be avoided by using genuine parts purchased from the OEM, like Genie® Genuine Parts.
Performance tracking
Some aerial fleet owners prioritize tracking downtime or even simply parts availability itself to indicate aerial reliability trends. These are closely related since waiting on parts to arrive and be fitted are the major cause of unplanned downtime. So, your ability to quickly order and receive OEM parts, as well as the age of units your OEM services are important factors for your equipment’s reliability.
Cost tracking
Tracking the cost of parts is also an indicator of the equipment’s total cost of ownership. An engine failure, or sometimes just a pump replacement, may be a signal that the cost of ownership curve is no longer sufficiently profitable. Although some engines may have an advertised life of around 8,000 hours, boom tubes and the chassis don't wear out unless damaged, so it's a misconception that machines simply have a standard maximum age or hours of life — these types of parts failures are often a sign of poor maintenance and can signal future issues.
The reality is that following best practices for the care of your MEWP fleet can save your rental business a lot of money. By completing the steps outlined in these tips, you can positively impact the residual value and on-the-job performance of your MEWPs, as well as will influence your customers’ perceptions of your rental business and equipment.
Related Posts
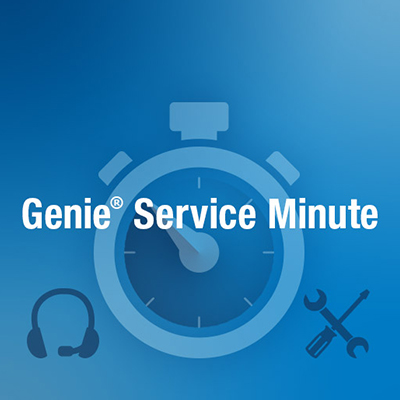
Service Minute: The Importance of Technician Training Programs
Training in the aerial industry is very important — a life is at stake each and every time someone gets into a piece of aerial equipment.
Continue Reading
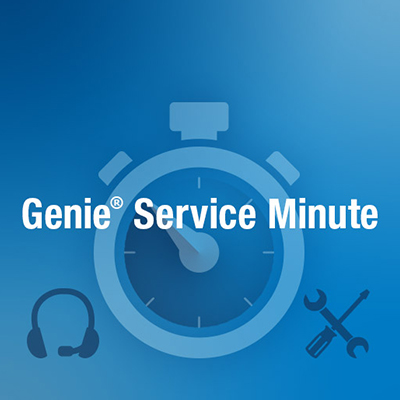
Service Minute: Repair Guidelines for Water-Damaged MEWPs
Water damage due to submersion or other extreme water exposure can be harmful to a mobile elevated work platform (MEWP).
Continue Reading
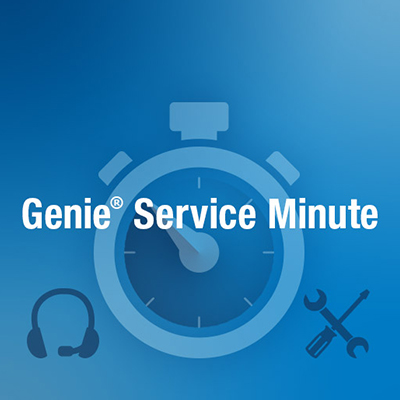
Service Minute: The Value of a Certified Aerial Equipment Service Technician
Your aerial equipment fleet is a huge investment for your rental company, so it’s important that your service technicians are properly trained to perform the necessary maintenance and repair work needed to keep your investment up and running.
Continue Reading