How Genie Stage V Engines Limit Downtime, Simplify Maintenance and Protect Engines
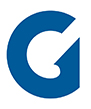
by Genie On Jul 9, 2020, 03:00 AM
Subscribe To Aerial Pros
Filter by tags
When Stage V engine standards took effect in the European Union as of January 1st, 2019, it impacted the majority of Genie® machines, including GTH™ telehandlers, higher horsepower S® and Z® boom lifts and GS™ rough-terrain scissor lifts. As an original equipment manufacturer (OEM), the latest date for Genie to produce according to the new standards is July 1st, 2020. The deadline for full distribution for Stage V machines 1st January 2021. However these dates are still under re-evaluation by the European committee due to the COVID-19 situation.
To adhere to these new emissions standards, there has been a lot of development in Stage V engines, and these engines’ technologies, including the addition of a DPF on Genie® machines powered with 36 to 55 kW / 49 hp to 74 hp engines. And, exclusive to the Genie Stage V engine solution, these engines now feature innovative, “operator-friendly” technology that safeguards the engine and its components, including the DPF, as well as simplifies maintenance tasks, without any compromise to the machine’s power, performance or productivity.
The Role of the DPF on Stage V Engines
The DPF, or a diesel particulate filter, which is a component of these new engines, is engineered to reduce the number of particles, or pollution, emitted into the environment during engine operation.
When a Stage V engine’s DPF is full of particle matter (soot from harmful substances in engines’ exhaust gases), it requires cleaning through a process called regeneration.
Passive regeneration occurs automatically when engine temperatures are high and soot levels have increased but are below the 100% soot threshold. During this process, the operator may notice only slightly higher engine speed but no noticeable degradation in performance.
Active standstill, or forced, regeneration occurs when the operator choses to do a manual regeneration cycle.
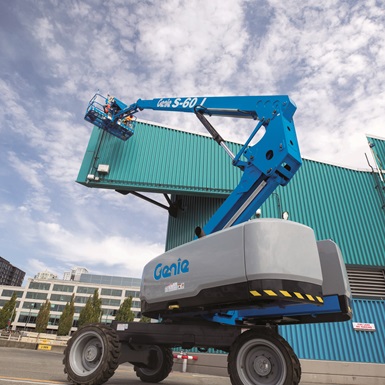
The Genie Stage V Engine Solution
In anticipation of incorporating these new engines into our equipment, we worked with our engine suppliers to introduce an exclusive Stage V engine solution for Genie machines that incorporates an innovative regeneration technology that safeguards the engine and the DPF — without any compromise to the machine’s power, performance or productivity.
This means that Genie Stage V engines include a proprietary “smart” regeneration software that is developed to actively monitor the level of soot in the DPF and notify operators that a regeneration cycle is needed. Thanks to a display on the Genie machine, operators will be able to see the DPF’s current soot level, as well as activate the regeneration process — in advance of the DPF becoming “full.” This capability allows operators to select a convenient time to run an active regeneration cycle, minimizing impact to jobsite productivity and machine performance. It also mitigates the risk of damage to Stage V engines and DPF because regeneration isn’t postponed past the engine’s limits.
The Genie smart regeneration technology has four active alert levels that notify operators that a regeneration cycle is needed. Here’s how it works:
- Level 1: High soot levels (100%) have been reached, time to schedule a regeneration cycle.
- Level 2: Slow down the boom hydraulic functionality speed by 30%; only allows “turtle” speed and blocks multifunction operations.
- Level 3: Slow down the boom hydraulic functionality speed by 60%; only allows “turtle” speed and blocks multifunction operations.
- Level 4: Stowed disable functions; the machine will only allow “turtle” speed.
The soot level and alert levels of their Genie Stage V engines can also be checked via the Genie Lift Connect™ telematics solution, which provides the real-time status of the DPF’s condition.
Because the current regulations do not force the engine to stop machine operation when the soot level is high, this can turn into downtime due to costly engine repairs or failures if the engine’s regeneration needs are delayed or ignored. So, we engineered the smart regeneration feature into the Genie Stage V engine solution to give equipment owners and operators peace of mind knowing that they do not have to worry about how to manage the regeneration process on Stage V engines — we’ve made it so that the machine does it for them. This means that our smart regeneration technology will continue to decrease the machine’s performance until a regeneration cycle is started to protect the DPF from damage or failure.
Other Features of the Genie Stage V Engine Solution
Stage V emission standards have been implemented to address the growing need in Europe for off-road engines to be more environmentally friendly, including cleaner burning, quieter operation and producing less vibration. These new engines are not only engineered to offer a significant reduction in particulate matter, NOx and HC, which results in a cleaner burning engine that emits less particulate matter, or pollution, into the environment, but these engines are also designed to run quieter, reducing real total engine noise output and presenting a smoother engine tone.
In terms of performance, all Genie machines equipped with our exclusive Stage V engine solution are designed with a turbocharger to maintain similar power and torque levels as compared to their Stage III counterparts. And, when possible, due to either lighter weight machines, like the Genie J series booms, or efficient hybrid systems, the Genie fuel-electric (FE) booms, a smaller Stage V compliant engine (under 19 kW / 25 hp) is selected, keeping the same performance as their “big brother’s” engine.
We purposely innovated the Genie Stage V engine solution to be powerful and productive, and thanks to their proprietary smart regeneration features, these engines will continue to perform in the field, day in and day out.
Related Posts
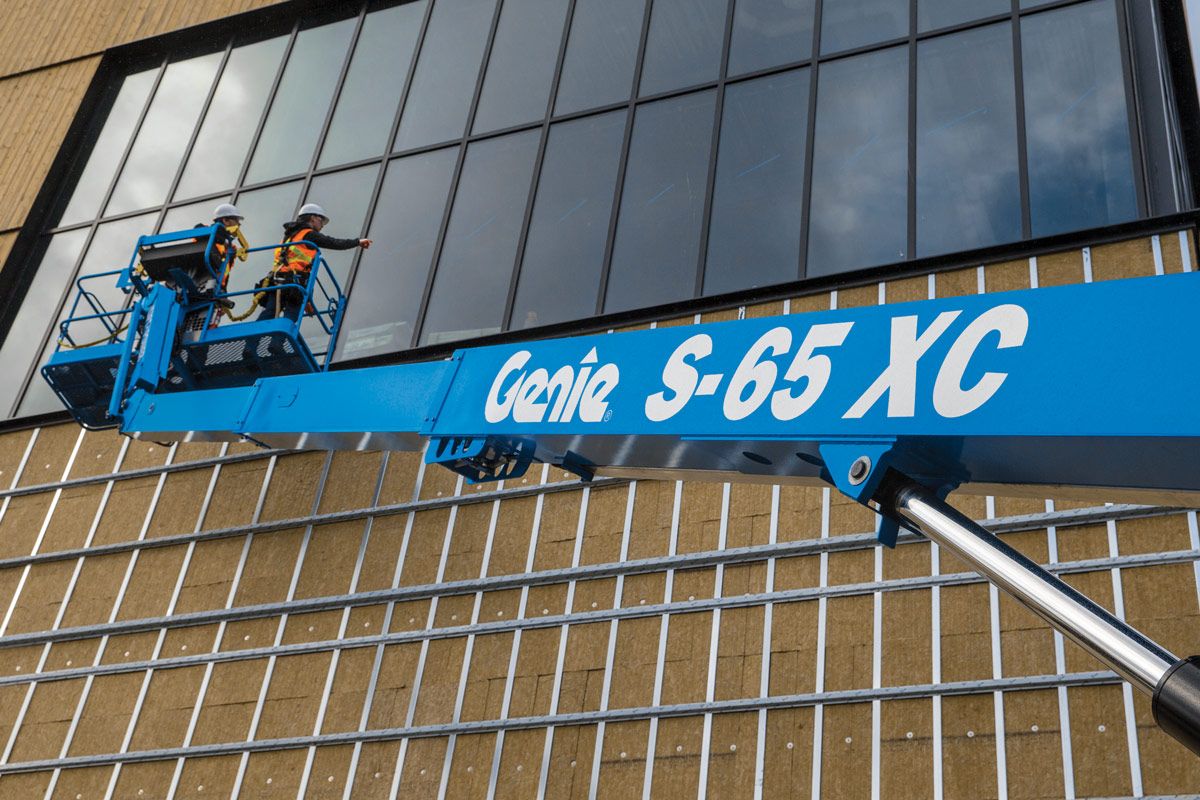
Understanding the New European Stage V Emissions Standards
Over the past two decades, the European Union (EU) has adopted a series of seven directives to address exhaust emissions for engines used in non-road equipment like telehandlers, boom lifts and scissor lifts.
Continue Reading
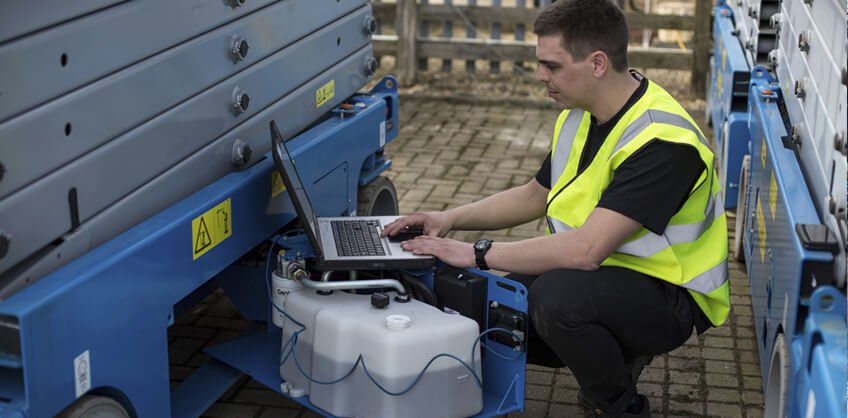
It’s Time to Embrace Telematics — Here’s Why
From reading about it in countless articles within trade magazines to conversations with peers, it’s easy to understand that telematics can bring a lot of benefits to rental businesses.
Continue Reading